Personal Reflection
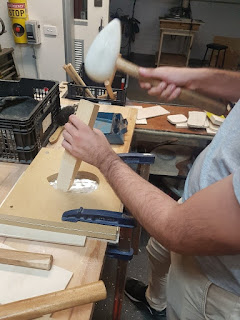
Personal Reflection The project that I have chosen it critically review which had revealed my strengths, weaknesses and thought processes in completing the best piece of work throughout the course was the blister. The reason why I have chosen this is because it required myself to think about different ways in which I could be completing my blister to perfection. The weaknesses that I had encountered when completing this module of the course was trying to think of shapes to hit around the corners of the blister to give it the shape. Therefore, I decided to make a corking tool that I was able to hit the edges of the blister, so I can make the depressions of the blister. With the corking tool I had to be very careful as I didn’t want to stretch the edges of the sheet metal that it would begin to tear. The strength that I had found out when I completed this blister, was that earlier in the semester when we completed the bowl, we had to use the radius to measure ci